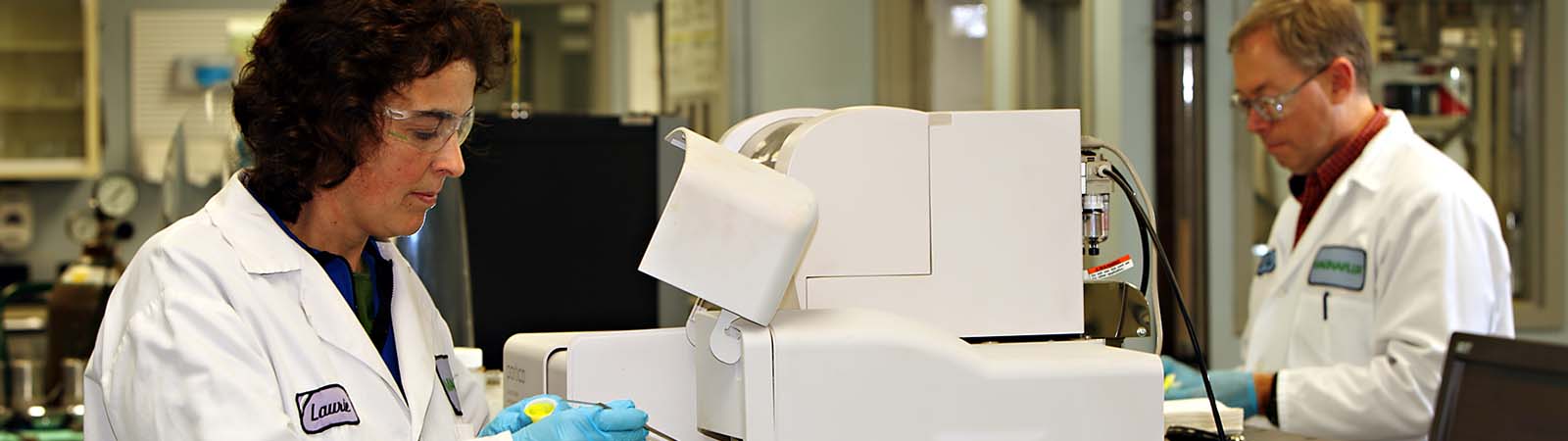
PeneCert™ Test Services for Liquid Penetrant Testing
- Causes of liquid penetrant contamination and degradation
Some facilities apply penetrants on a one-off basis; others store penetrants in closed tanks or containers until used. However, most facilities use the immersion method, where excess penetrant is allowed to drain back after application to the part being tested. With the immersion method, tanks are often open to the environment, which increases the risk of contamination. Coupled with this contamination can be introduced from the part(s) under test.
Common Causes of Liquid Penetrant Contamination
- Water
Contamination from water is the most common form of contamination. The water can come from pre-washed parts that are not fully dried, careless rinsing or from leakage from pipes. Water contamination is not generally a risk until the point where the water tolerance of the penetrant is met.
- Dirt and insoluble solids
Dirt and insoluble solid contamination can result from poor cleaning or allowing contaminant materials to fall into the tank.
- Organic material
Oils, lubricants, paints, greases, organic solvents, cleaning solvents and degreasing fluid are all sources of organic material contamination. Whilst penetrants are able to absorb amounts of oils and solvents, their level of fluorescence will be decreased and the penetrant washability will also be affected.
- Alkaline cleaners and acids
Alkaline cleaners and acids represent the most serious type of contamination as they destroy fluorescence when they come into contact with a penetrant. In addition, some alkaline cleaners contain metasilicates, which can prevent penetrants from entering and therefore detecting a crack.
Causes of Liquid Penetrant Degradation
- Heat
In some cases heat can be used to speed up the action of a penetrant. However, prolonged exposure to temperatures over 60 °C can reduce the fluorescence of a penetrant. Temperatures in excess of 120 °C will destroy fluorescence completely.
- Evaporation
Penetrants stored in open tanks will undergo continuous evaporation, especially if the tanks are large and exposed to warmer temperatures. Evaporation may cause an increase in viscosity, which would subsequently increase the time taken to remove the penetrant.
- Faulty equipment
Un-calibrated or faulty equipment and accessories can compromise penetrant systems. For example, drying oven thermostats or controls that are set improperly set can lead to incorrect oven temperatures. Similarly water pressure gauges can malfunction or the UV output from black light bulbs can be reduced with aged bulbs.
The effects of contamination and degradation will depend on the type and amount present. Any change in colour or consistency should be addressed immediately to ensure consistent inspection results.
- Liquid penetrant testing service options and guidelines
Penetrant system testing can be performed in-house or using an external service. ASTM E1417 has established standards for performance checks for in-use materials.
In-Use Penetrant Test Requirements |
ASTM E1417 |
System Performance |
Daily |
Penetrant Contamination |
Daily |
Developer Contamination (Soluble and Suspendable) |
Daily |
Developer Concentration (Soluble and Suspendable) |
Weekly |
Developer Condition - Dry Powder |
Daily |
Water Content (Water Washable only) |
Monthly |
Emulsifier concentration (Hydrophilic Only) |
Weekly |
Penetrant Sensitivity |
As required per 7.8.3 |
Fluorescent Brightness - Measured Brightness |
Quarterly |
Emulsifier Water Content (Lipophilic only) |
Monthly |
Penetrant Removability (Water Washable only) |
As required per 7.8.3 |
Emulsifier Removability (Lipophilic and Hydrophilic) |
As required per 7.8.3 |
Facilities that do not have the instrumentation or resources to carry out on-site testing can opt to use the Magnaflux PeneCert Service.
- How to use the PeneCert Liquid Penetrant Testing Service
- Get a quote: Contact us for a price quotation for your PeneCert service.
- Collect samples: For each in-use material to be tested, collect at least 500ml sample.
- Label bottle(s): Fill out a label and attach to the appropriate sample bottle(s). Please ensure that each bottle cap is tightened securely.
- Complete form: Fill out a PeneCert menu form, indicating the testing that you require. If you are sending more than one sample of penetrant, please complete one form per sample.
- Send samples: Send your samples to: Aerotech Laboratories Ltd, (Magnaflux PeneCert), Unit 20, Mercia Business Village, Westwood Business Park, Coventry, CV4 8HX, UK.
- Results: We will email you the test results as soon as they are available.
- Invoice: Invoices will be issued from the Magnaflux office in Swindon, UK.
Please wait while we gather your results.
Read More About Test Services for Penetrant Inspection
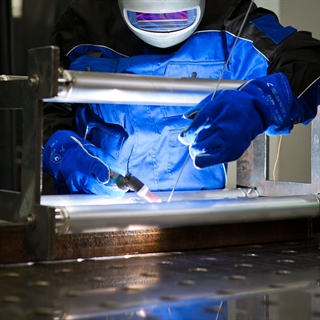
Secondary processing and finishing discontinuities are associated with the various finishing operations, after the part has been rough formed by rolling, forging, casting or welding.
Read More...
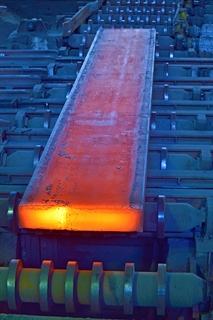
When steel ingots are worked down into usable sizes and shapes such as billets and forging blanks, some inherent discontinuities may appear.
Read More...
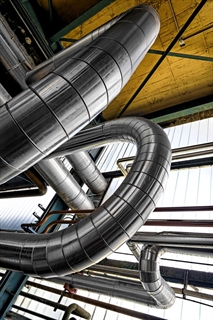
Service discontinuities are formed or produced after all fabrication has been completed and the part has gone into service.
Read More...
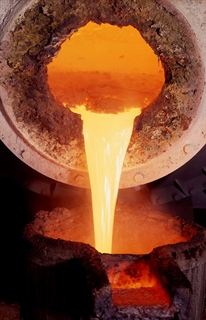
While one might assume defects or abnormities occur during a part’s manufacturing process, there are some discontinuities which occur before a part’s creation even starts.
Read More...
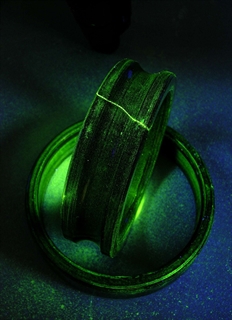
In the world of nondestructive testing, “defect” and its synonyms are not necessarily interchangeable.
Read More...
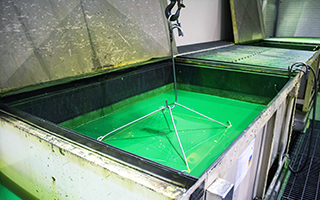
Learn how liquid penetrant testing products lose performance over time and what to do to ensure penetrant test reliability.
Read More...
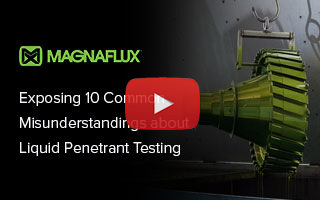
We reveal common misperceptions about liquid penetrant inspection we’ve seen in the field in recent years
Read More...
![The Ultimate Guide to Fluorescent Penetrant Testing [Infographic] The Ultimate Guide to Fluorescent Penetrant Testing [Infographic]](/Files/Images/Blog-Images/01282020-Titan-Thumbnail.jpg)
Liquid penetrant inspection is a nondestructive test method which does not harm the parts being inspected.
Read More...
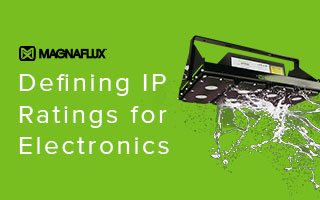
In this article, we break down the ANSI/IEC 60529 Ingress Protection Code with a chart to show what's essential for NDT equipment
Read More...
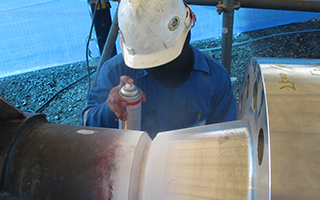
Learn about the available properties of developers and the relationship between dwell time and inspection quality
Read More...
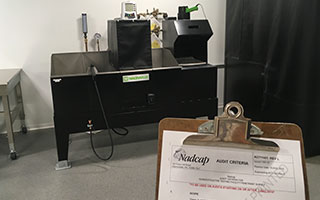
Properly demonstrating the system performance check was the #2 Nadcap audit finding for penetrant systems. What do you need to do to comply?
Read More...
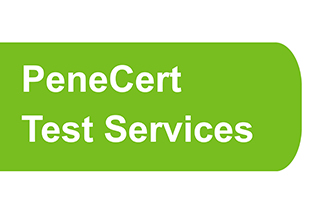
Learn more about test services for in-use penetrant, emulsifiers and developers to comply with ASMT E1417 and AMS 2644.
Read More...
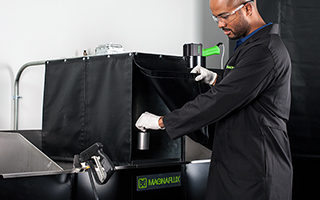
Learn the differences between type testing, batch testing and in-use testing for NDT liquid penetrants.
Read More...
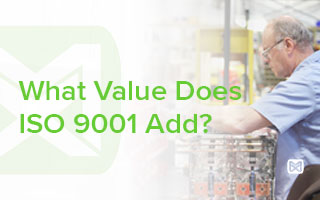
Learn how ISO 9001 affects the NDT materials you use, therefore affecting your quality management system
Read More...
You want the best solution for your application. We can help you find it.