Precleaning is the first step in any penetrant inspection. However, the role precleaning plays in a reliable, accurate LPI inspection is often underestimated.
In some facilities, precleaning operations may not be part of the NDT department and may be physically located considerable distances from the penetrant lines, making it difficult to coordinate the precleaning and penetrant inspection processes.
Nevertheless, it is essential that parts are clean and dry prior to penetrant application. Parts must be free not only of oil, grease, and particulates, but also cleaner residue.
Cleaner residue can impact the outcome of a penetrant inspection in much the same way that an oily, dirty part can. Penetrant works by locating surface breaking defects so any substance that might fill the defect, including cleaner residue, must be removed from the part prior to penetrant application.
Parts typically require a clean water rinse to completely remove residues. After the clean water rinse, parts must be thoroughly dried because water can block entry of penetrant into surface breaking defects since penetrant cannot displace water or penetrate through water into defects. Oven drying is often recommended to remove water because air drying and flash drying may not produce completely dry parts, especially in high humidity conditions.
Proper precleaning can have a significant effect on the successful outcome of a penetrant inspection. Below are two examples of how improper precleaning can impact PT test results.
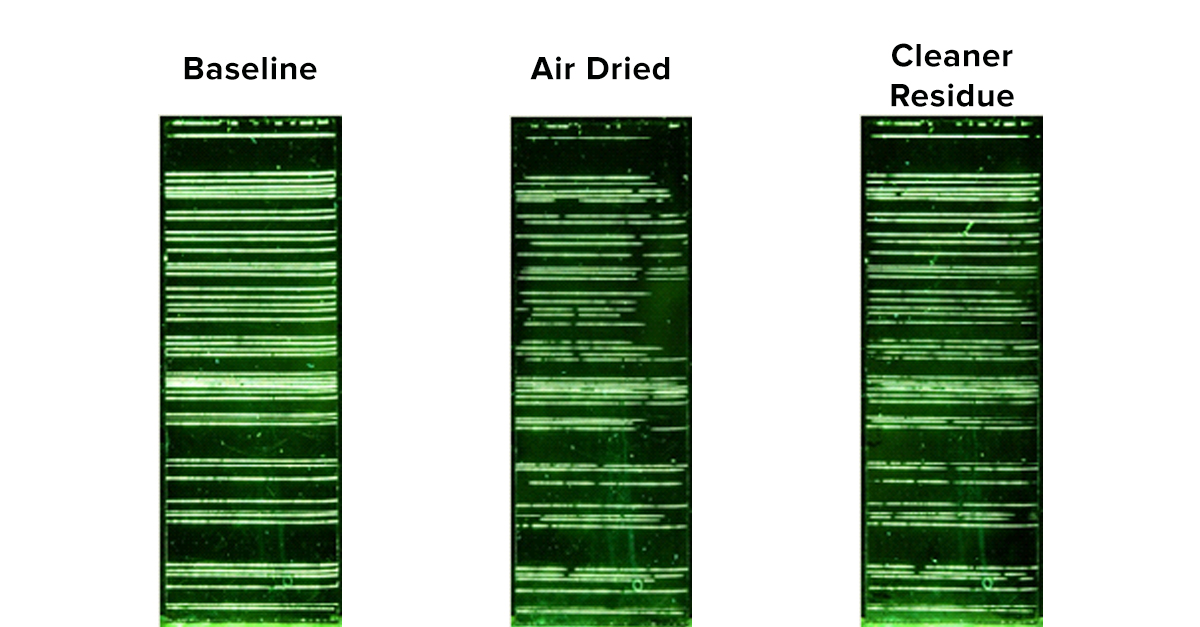
The baseline panel result included proper precleaning process (complete rinsing of cleaner residue with clean water followed by thorough drying in hot air circulating oven dryer).
Compared to the baseline, air drying impacts the penetrant sensivity and brightness, possibly because water pools with the penetrant in defects and downgrades the penetrant sensitivity and brightness.
Incomplete rinsing of cleaner residue also impacts the penetrant sensitivity and brightness, as viewed in the right most photo.
Removing any residues from parts prior to penetrant application also prevents contaminating the penetrant in tanks and avoids costly downtime and penetrant replacement.
Alkaline cleaner residues and mineral precipitates from some cleaners can mask discontinuities, cause excessive background on parts, and potentially degrade the fluorescent brightness of penetrants.
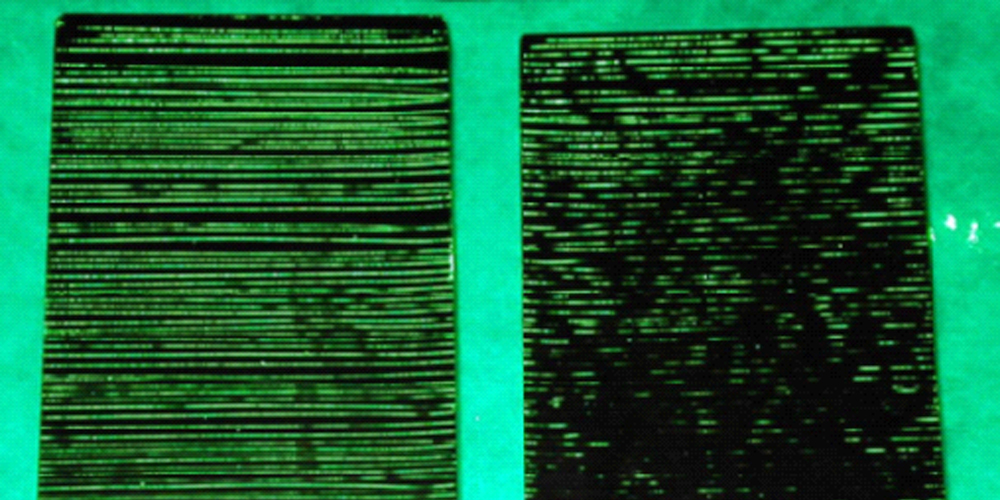
This photo also compares standard penetrant process to penetrant contaminated with alkaline cleaner residue. Notice the effect of residual cleaner on both the penetrant sensitivity and fluorescent brightness.