Learn about the function and importance of UV-A pass filters, and why ASTM E3022 requires all LED UV lamps to have them
The quick answer to, "Why should a LED UV black light have a UV-A pass filter?" is because UV-A pass filters reduce glare and increase contrast of fluorescent indications. Which makes fluorescent inspection easier, faster and more reliable.
In this article, we will explain why a UV-A pass filter is needed, and how the pass filter works to create better UV irradiation for nondestructive testing inspection.
Why do LED UV lamps need a filter?
From a technical point of view, ASTM defines UV-A as 320-400 nm, and visible light as 400-760 nm. The emission spectrum of an UV-A LED is a single peak in the 360-370 nm range. But this is not a tight, sharp peak, and at the tail end of the emission spectrum you get measurable emission above 400 nm.
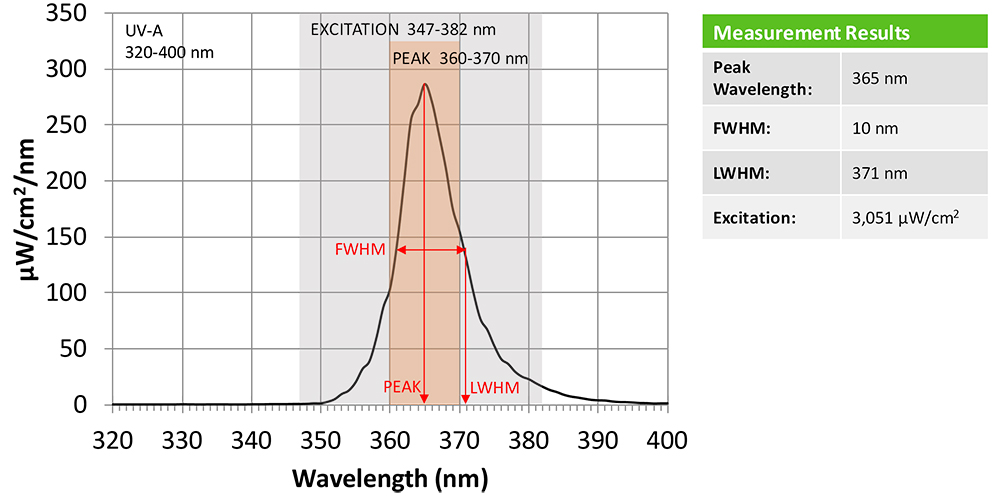
Tail emission above 400 nm is a very small amount of light compared to the bright UV-A peak, but it is visible as a deep violet glow on the surface.
Using a calibrated laboratory spectroradiometer, tail emissions can be measured and characterized by the UV lamp manufacturer. However, the standard NDT visible light meters which are typically used to check ambient light in an inspection area are not capable of accurately measuring tail emissions; abnormally high readings may be seen even when the actual visible light levels are below 2 ft-candles or 20 lux.
How a UV-A Pass Filter Works
Instead of creating an all-new method for fluorescent NDT practitioners to monitor their LED UV-A lamps, ASTM E3022 requires the UV lamp manufacturer to include a UV-A pass filter in each LED UV lamp. The pass filter acts to remove tail emissions above 400 nm, which eliminates the accuracy issue with NDT visible light meters.
Since tail emission is visible as deep violet light, adding the UV-A pass filter eliminates the glare and makes the background of the part surface darker. This increases contrast between fluorescent indications and the darkened part surface when using fluorescent magnetic particle or penetrant techniques.
Glare can also mask small indications, and the inspector may need to reposition the part multiple times to view the entire surface. Elimination of glare simplifies part handling and saves time during inspection.
In high volume production, small changes can multiply into large improvements. Faster detection means more parts inspected during a shift. A few seconds of improvement can mean the difference between NDT acting as a bottleneck and smooth-running operations.