- Why would I choose liquid penetrant inspection?
Liquid penetrant inspection (LPI) is a simple, cost-effective and reliable method of non-destructive testing that can be used for the inspection of surface-breaking faults on a wide variety of non-porous material types, including metals and ceramics. Unlike magnetic particle inspection (MPI), LPI can be used for the inspection of non-ferrous metals.
The nature of the technique lends itself well to the inspection of large areas and parts, and the inspection of complex geometric shapes.
- What types of liquid penetrant inspection products does Magnaflux EMEA manufacture?
Magnaflux manufactures both UV fluorescent and visible penetrants.
Magnaflux fluorescent penetrants contain dyes that fluoresce when exposed to ultraviolet (UV) radiation. Our visible penetrants contain a red dye that provides high contrast when viewed against a white developer background.
- How are penetrants classified?
Under AMS 2644, penetrant systems are classified as:
- Type 1 – fluorescent penetrants
- Type 2 – visible penetrants
Penetrants are then classified by the method used to remove the excess penetrant from the part. The four methods are as follows:
- Method A – water-washable
- Method B – post-emulsifiable, lipophilic
- Method C – solvent-removable
- Method D – post-emulsifiable, hydrophilic
Water-washable (Method A) penetrants contain emulsifiers, which means they can be removed from the part by rinsing with water alone.
Post-emulsifiable penetrants can be removed using two different methods of emulsification, namely lipophilic and hydrophilic. A lipophilic emulsifier (Method B) acts by essentially changing the chemistry of a penetrant so that it acts like a water-washable penetrant, thus allowing the excess penetrant to be removed using water. A hydrophilic emulsifier (Method D) works like a detergent by emulsifying the excess penetrant so that it can then be removed using water, in the same way that fat from cooking meat can be emulsified with liquid detergent to enable it to be washed away with water.
Solvent-removeable penetrants require the use of a solvent (Method C) to remove the penetrant from the part.
Penetrants are then classified based on their ability to detect an indication. The five sensitivity levels are as follows:
- Level ½ – ultra low sensitivity
- Level 1 – low sensitivity
- Level 2 – medium sensitivity
- Level 3 – high sensitivity
- Level 4 – ultra high sensitivity
- How do I decide whether to use a UV fluorescent or visible penetrant?
In many cases, the particular penetrant inspection technique, and therefore the choice of penetrant type, will be dictated by a procedure relevant to the part being inspected. This is particularly common within the aerospace sector, where there are strict guidelines associated with NDT inspection. In other industry sectors, this will be less strict.
Often, the choice as to whether to use a UV fluorescent or visible penetrant will come down to a number of factors, including the following:
- The nature and size of the part(s) to be inspected.
- The number of parts to be inspected. For example, clients that are inspecting a large number of parts as part of a production operation invest in a penetrant line incorporating fluorescent dye penetrant.
- The environment where the inspection takes place, i.e. indoors or outside in the field. For example, testing welds on a pipeline in a desert would favour the use of a visible penetrant.
- The nature of the faults to be detected. For example, small difficult-to-find faults would favour the best inspection conditions, which would be a darkened area using a UV fluorescent penetrant.
- How do I decide which sensitivity level of penetrant I should use?
Penetrant sensitivity is a complex area. Whilst it relates to the ability to find indications, other factors play a key part too. For example, on a rough casting a high sensitivity penetrant would be difficult to remove from the background areas, so you would look to use a low sensitivity penetrant. Conversely, with a polished titanium part, you would use a high sensitivity penetrant so you can be sure that the penetrant will remain present in any flaws after the washing process.
Different industries have different requirements in relation to penetrant sensitivity. However, as a general rule of thumb, you should look to use a low sensitivity penetrant on rough parts, a medium sensitivity penetrant on general engineering components, and a high sensitivity penetrant on more precision or polished components.
- What is the sensitivity of a visible penetrant?
The typical sensitivity of a visible penetrant is Level 2, as dictated by the EN-ISO 3452-2 standard.
- What is the difference between Type testing, Batch testing and In-use testing?
Type testing
When seeking approval for a penetrant in accordance with material specifications such as AMS 2644 and EN ISO 3452-2, the penetrant manufacturer is responsible for getting the product Type tested. This involves sending a sample of the penetrant off to an independent laboratory for verification against a comprehensive set of standard tests.
Batch testing
During the routine manufacture of a penetrant and its associated consumable products, it is a requirement under material specifications such as AMS 2644 and EN ISO 3452-2 to carry out a number of batch-specific tests, including flash point, viscosity and fluorescent brightness (Type 1 systems only). These specifications also specify the sampling rate and dictate that we should publish these results on a certificate of conformance. For Magnaflux EMEA penetrants, cleaners, developers and emulsifiers, these certificates of conformance are referred to as Batch Inspection Certificates.
In-use testing
When a penetrant is being used, there are a set of in-use tests that need to be carried out by the customer. ASTM E1417 has established standards for performance checks for in-use materials. You can find out more information on these tests here, where you will also find details of our PeneCert testing service, whereby in-use tests are carried out using an independent laboratory.
- How is the sensitivity level of a penetrant defined?
The sensitivity of a penetrant is not just simply its ability to find different sized cracks/defects; it also relates to aspects such as the type of surface finish. For example, on a rough casting you would not want to use a high sensitivity penetrant as it would be too difficult to remove, and you would see a lot of penetrant in the background. Conversely, on a highly polished part you would not want to use a low sensitivity penetrant as the risk of over washing and removing penetrant from the cracks/defects would be high. The sensitivity of a penetrant is ultimately determined by the independent laboratories that assess the penetrant in accordance with material specifications such as AMS 2644 and EN-ISO 3452-2.
- With ZYGLO fluorescent penetrants, why would I use a post-emulsifiable penetrant over a water-washable penetrant?
Post-emulsifiable penetrants are a better choice if you are concerned about removing too much penetrant from a part due to over-washing. These penetrants require a separate emulsifier to break them down and make them water-washable; as such, you have better control over the washing process. Of the two emulsification processes – lipophilic and hydrophilic – hydrophilic removers give you better control over the removal of the penetrant as they are less sensitive to the contact and removal time. For this reason, the lipophilic post-emulsifiable method is now virtually obsolete.
- What do the terms PE and PR mean in relation to removing post-emulsifiable penetrants?
The acronym PE refers to the lipophilic method (Method B) for removing post-emulsifiable penetrants.
The acronym PR refers to the hydrophilic method (Method D) for removing post-emulsifiable penetrants.
- When using Method D (post emulsifiable, hydrophilic), do I need to check the quality of the ZR-10C remover/emulsifier from time to time?
ZR-10 is supplied as a concentrate which needs to be diluted with water to its working concentration. Before using the diluated ZR-10C solution, we recommend carrying out refractometer meetings, described in the Product Data Sheet, to create a ZR-10C concentration chart. Typically, we recommend a working concentration of around 20%. With low concentrations (for example, 5%), the emulsifier will tend to become saturated with penetrant over a short period of time. You will see this as a distinct separation of the penetrant floating on the top of the remover bath. At this point, it will no longer be possible to emulsify and remove the penetrant, and you will need to remake up the bath with a fresh solution. Using a higher concentration (up to 20% ZR-10C) will mean that the bath life should be significantly longer, although it will still need to be replenished at the point where the bath becomes saturated with remover.
- With fluorescent penetrants, is it possible to remove the excess penetrant using a solvent wipe technique?
From a practical point of view, it is not always possible to remove penetrant using a water-wash or post-emulsification process. For example, this may not be practical:
- if you are inspecting a small part;
- if you are applying the penetrant using an aerosol;
- if the location of the inspection is distant from a source of water or a facility to collect and process the rinse water.
In these instances, it is possible to remove the excess penetrant using a solvent wipe technique.
To perform this method of removal, apply the solvent (for example, SKC-S) to a cloth, and then perform one or two gentle wipes across the surface of the part to remove the excess penetrant. With each wipe, ensure that a clean area of the cloth is used. Take care not to wipe too hard or to wipe too many times as this could remove the penetrant from any faults that are present.
- What is the best alternative to an aerosol LPI penetrant that can be used in situations where flammability represents a hazard?
Use the bulk variant of the product (for example, SPOTCHECK SKL-SP2 and ZYGLO ZL-60C are available in aerosol and bulk variants), then apply the ink using a pump spray bottle.
- Is the pre-cleaning of parts important?
The way penetrant inspection works is by the penetrant liquid wetting the surface of the part and finding cracks and surface-breaking defects. This process will be inhibited by the presence of surface contamination such as grease, oil, metal treatment chemicals or even residues from previous inspections.
Pre-cleaning of parts is best done using a solvent-based cleaner. The action of the solvent will remove any residues from the surface and evaporates to leave a clean and dry surface.
When working in outdoor environments, the pre-cleaning process will also need to remove all traces of water, moisture and, at low temperatures, ice.
Magnaflux offers cleaners with different solvent make-ups to meet the requirements of our customers.
- What recommendations does Magnaflux offer about penetrant dwell times?
In our Product Data Sheets, we offer the following guide information on penetrant dwell times (penetration time, contact time):
‘Minimum penetration time is 2 to 5 minutes, with 10 minutes being adequate for most situations. Lower temperatures will thicken the penetrant and require longer penetration times’.
For our visible red penetrants, the following graph illustrates how the dwell time is affected by the temperature at which the inspection is carried out.
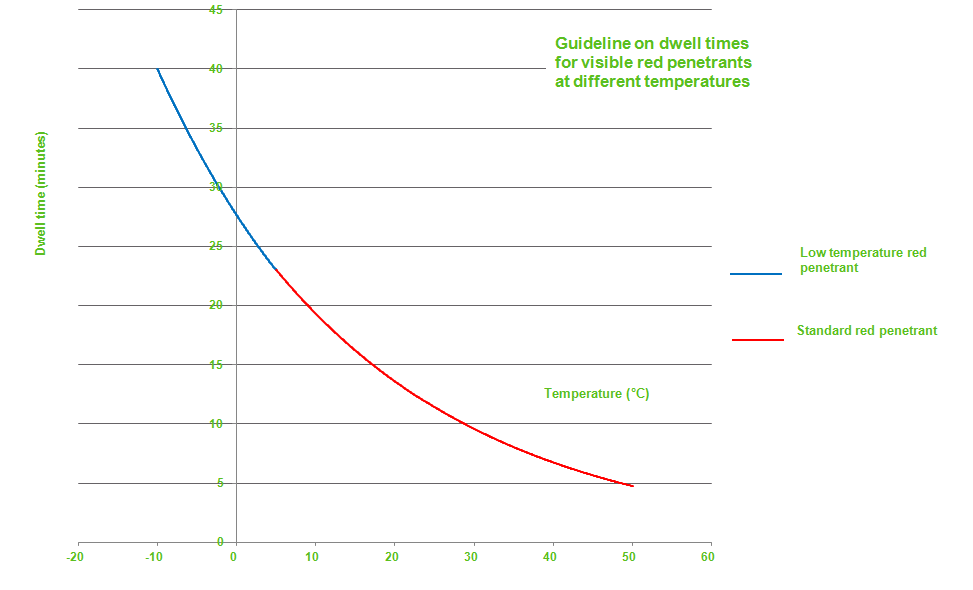
Please note that this information is for guidance purposes only. With any penetrant – fluorescent or visible – the penetrant dwell time will be dependent on the type of material (metals, plastics, ceramics, castings, forgings, rolled materials, welds, etc) as well as temperature.
Magnaflux recommends that prior testing is carried out when inspecting different material types, or when inspecting at different temperatures, to establish the most appropriate dwell time.
- What is the purpose of a developer?
The purpose of a developer is to effectively pull the penetrant back out of a defect to allow it to be seen by an inspector. The action of pulling it back to the surface also allows the penetrant to spread along the surface around the defect, thus magnifying the strength of the indication.
With UV fluorescent penetrants, the developer particles both reflect and refract the UV light, which makes the indications brighter.
With visible penetrants, the developer, in addition to pulling the penetrant back to the surface, creates a white background to create an ideal contrast between the indication and the surrounding surface.
- How do I decide which type of developer to use?
Under AMS 2644, there are four primary classifications of developer, namely:
- Form a – dry powder developer
- Form b – aqueous soluble developer
- Form c – aqueous suspendible developer
- Form d – non-aqueous wet developer for fluorescent penetrants
- Form e – non-aqueous wet developer for visible penetrants
Dry powder developers
Dry powder developers (ZP-4D) are generally considered to be the least sensitive. However, they are easy to use and inexpensive. They can be applied using the following techniques:
- Dipping
- Powder spray applicator – for example, powder spray bulb dispenser
- Powder storm cabinet
- Electrostatic spray gun
Water-suspendible developer
With a water-suspendible developer, the developer particles are suspended in water. It is important to keep the developer suspension stirred or agitated to prevent the particles from settling out of the suspension. After application of the developer, you will need to dry the parts to remove excess water. Water-suspendible developers can be applied using the following techniques:
- Spray
- Immersion dip
- Flow on
Water-soluble developers
With a water-soluble developer (ZP-14A), the developer particles are dissolved within a water carrier. After application, a film of developer will form on the surface of the part during the drying stage. As with water-suspendible developers, water-soluble developers can be applied using the following techniques:
- Spray
- Immersion dip
- Flow on
Non-aqueous developers
Non-aqueous developers are solvent-based, where the developer is suspended in a solvent-based carrier. Being solvent-based, there is no need for force drying as the solvent evaporates quickly from the part.
In general, these products are supplied and used as aerosols for convenience and ease of use. If used in bulk, they will need to be applied using a spray gun, with care being taken to keep the developer stirred/agitated.
- Can a solvent-based (non-aqueous) developer be applied using anything other than a spray technique?
Our solvent-based (non-aqueous) developers contain inorganic white pigments dispersed in a solvent mixture. When sprayed onto a component, the solvent evaporates to leave the fine layer of white developer particles. By their very nature, it is hard to keep these inorganic pigments in suspension; without agitation – for example, the shaking of an aerosol can – they will fall to the bottom of the container. This is why we recommend spraying, either by aerosol or conventional spray gun. However, it is possible to use a dip method, as long at the developer is thoroughly mixed before dipping the component into the developer.
- What is the best alternative to an aerosol developer that can be used in situations where flammability represents a hazard?
Our non-aqueous developers (SKD-S2, ZP-9F) are solvent based. However, it is possible to for a different type of developer, depending on the penetrant type, to be used:
Penetrant type |
Developer |
UV fluorescent penetrants |
Dry powder developer – ZYGLO ZP-4D
Water-soluble – ZYGLO ZP-14A |
- Can penetrants be used to inspect ceramic, plastic and/or composite materials?
Whilst Magnaflux penetrants can be used on ceramic, plastic and/or composite materials, the dyes within them can cause staining. It is also possible that the penetrant will soften or even dissolve the base material of some plastics.
A key point here is that the penetrants are only suitable for non-porous materials. We do not recommend their use on porous ceramic or composite materials. We strongly recommend that you carry out a pre-test with the penetrant when using such materials, in order to check the compatibility of the penetrant.
- Are there special precautions that I should take when carrying out penetrant inspection at low temperatures?
Magnaflux provides an online resource regarding the storage and usage temperatures for its products. Taking an example, for SKL-WP2 we quote a usage temperature range of -5°C to +50°C. In this range, the characteristics associated with the product as supplied – for example, viscosity – will be at their optimum.
However, we cannot know the actual conditions present during an inspection which might affect the product performance. When operating below 10°C the following risks are presented:
- The presence of moisture in the form of condensation, frost or ice. Below -5°C this situation becomes a higher risk as any moisture will be present as ice. At the very least, all moisture, frost and ice must be removed prior to carrying out a test.
- Differences between the air temperature and the temperature of the component to be inspected. For example, if an inspection is being carried out on an external vessel, the air temperature within that vessel is likely to be higher than the temperature of the vessel wall.
- Differences in the structure of the component to be inspected. For example, as a general rule metallic structures will contract as the temperature becomes lower, and different metals contract at different rates. This contraction effect could mean that any surface-breaking defects at lower temperatures are potentially finer, and may be harder to detect.
- The penetrants are likely to have lower mobility into a defect. As a resul,t the test times – in particular penetration times – may need to be lengthened.
For all of these reasons, we strongly recommend that any inspection carried out at temperatures <10°C is subject to an application test using known test materials/reference materials, that will validate the test results under these conditions.
- When a penetrant is only available in bulk liquid format, what methods can be used to apply it to a component?
The penetrant can be applied using the following techniques:
- Immersion dip
- Brush (painting)
- Flow on
- Conventional spray – air gun or pump spray bottle
- Electrostatic spray
- Does Magnaflux still manufacture and supply penetrant pens?
No, we discontinued our penetrant pens as they were prone to leaking during transportation.
- Where can I find information on the level of chloride, fluoride, sulphur and sodium within penetrants and their associated cleaners and developers?
The traditional non-destructive testing specifications for the aerospace sector require us to test for the levels of contaminant – including halogens (chloride and fluoride), sulphur and sodium – within our penetrants and their associated cleaners and developers.
You can find information relating to the maximum permittable levels within our Product Data Sheets. However, during our routine quality control testing, we carry out specific testing on each batch of material for chloride, fluoride and sulphur levels. The amount of information we provide is dependent on the product/specifications, and is presented in our Batch Inspection Certificates – see example below.
EXAMPLE: ZL-67B, batch number: 1501033
Test method |
Magnaflux test result |
General aerospace specification limit |
Pratt & Whitney specification limit |
Chloride content |
8 ppm (0.0008%) |
< 300 ppm |
< 400 ppm |
Fluoride content |
1 ppm (0.0001%) |
< 50 ppm |
< 50 ppm |
Sulphur content |
10 ppm (0.0010%) |
< 300 ppm |
< 1000 ppm |
Sodium content |
15 ppm (0.0015%) |
< 100 ppm |
< 100 ppm |
Some points to note:
- The actual recorded values, whilst varying from batch to batch, are significantly lower that those defined within the aerospace limits.
- The contaminant levels that we quote are attributable to very low levels of contaminant which are present within raw materials that we use to make our products. To give a scale for this, if an end user was using normal tap water it is possible that they could be adding a significantly higher level of chloride to the process – the EU’s drinking water standard is 250 mg/litre, which equates to 0.025% (250 ppm).
- Most specifications require test results as percentage values, although a few require parts per million (ppm). To convert percentage concentration to parts per million (ppm), multiply by 10,000; to convert parts per million (ppm) to percentage concentration, divide by 10,000.
- MIL-STD-271, MIL-STD-2132 and ASME Sec V all require that materials to be tested are subject to a procedure to evaporate off volatile solvents before analysis for halogens and sulphur. According to these specifications, only those residues higher than 0.005 g/100ml shall be analysed for halogens and sulphur. Where the residue figure is below 0.005 g/100ml, it is reported within the Batch Inspection Certificate. For this reason, you will often not see results for sulphur and halogen results quoted for products such as our cleaner SKC-S, where the residue value is so low.
- When I receive Magnaflux product in a sealed barrel, what tool do I need to open it?
To open these barrels, you will need a Tri-sure spanner. These often come with a tab seal cap remover.
- What is the best way to get product out of a sealed 25 or 200 litre barrel?
The best way to get the product out of these barrels is to use a threaded barrel pump that screws into the main opening. On the top of a Magnaflux barrel, you will typically see two openings – the main opening is 2 inches (50.8mm) in diameter (2″ BSP) and the smaller breather hole is 0.75 inch (19.1 mm) in diameter. Before pumping the liquid out, you will need to unscrew the seal on the breather hole.
Barrel pumps come in a variety of power source types. Most are hand operated but it is also possible to source battery and electric pumps. They also come in a number of different styles – lever pumps, lift pumps, rotary pumps and syphon pumps. Some have telescopic tubes on which enables them to used with different barrel sizes. We would recommend using one with Viton seals. Viton is a brand of synthetic rubber and fluoropolymer elastomer which provides good chemical resistance to a wide range of liquids, including Magnaflux LPI and MPI products. It is not uncommon to be able to replace these seals.
- How can I remove penetrant residues from the component(s) I am inspecting?
If a component is found to have cracks and surface breaking defects, or is relatively porous, penetrant residues are likely to be present following the inspection process. Penetrant residues can be removed using one of the following techniques:
Water wash: It may be possible to remove penetrant residues from component(s) using further water washing – applicable to water-washable penetrants and post-emulsifiable penetrants (the latter would also require the use of an emulsifier).
Solvent wipe using a remover: It may be possible to remove penetrant residues from component(s) using a solvent wipe technique – applicable to all penetrants. In this case, the remover – for example, SKC-S – is applied to a cloth which is then used to wipe the component surface.
Solvent soak: This process involves the use of solvents in liquid form to clean the component(s) and remove the penetrant residues. Using this method it is possible to soak the component(s) in a cleaner – for example, SKC-S. Alternatively the component(s) can be soaked in an alcohol (for example, isopropyl alcohol) or a ketone (for example, acetone). Use of an ultra-sonic bath will further enhance this process. In all cases, this process would require a risk assessment.
Vapour degreasing: This process involves the use of solvents in vapour form to clean the component(s) and to remove the penetrant residues. This process works on the basis that the solvents will solvate the penetrant and thus remove it from any surface defects or pores. The use of solvents in vapour form is one that poses a higher health and safety risk and as such Magnaflux EMEA recommends seeking the advice of a company specialising in this technique and to carry out a risk assessment.
To check for removal of any penetrant residues:
- A visual inspection should be used for red visible penetrants.
- Inspection using a UV(A) light source should be used for fluorescent penetrants.
- Does Magnaflux have any recommendations on how to remove penetrant residue from test panels?
Over time, penetrant residue can build up within test panels, which will affect their performance. Also, in a hard water area, it is possible to get salt and limescale deposits within the panels. Our recommendations on cleaning are:
- Pre-soak the panels in hot water (ca. 50-70ºC) for a few minutes. This will soften any residual penetrant.
- Use a polar solvent such as acetone, methyl ethyl ketone (MEK) or isopropanol in combination with an ultrasonic bath. This way you get a combination of the solvent action and also a vibrational effect to release any residues. Prior to doing this, we recommend that you carry out a workplace risk assessment to minimise or eliminate any risk to an operator.
- If you are in a hard water area, you could also use a weak solution of a limescale remover. Avoid using strong acids or prolonged contact with a limescale remover as this will cause damage to the chrome plating. Ensure that all traces of limescale remover are removed by rinsing with deionised water.
- Ensure that the panels are fully dried before reusing.
- How should I dispose of empty aerosol cans?
Although, in the UK, aerosols are not a category of Hazardous Waste under the Lists of Wastes Regulations 2005, materials containing flammable solvents and/or flammable aerosol propellants are classed as Hazardous Waste. As a result, empty Magnaflux EMEA aerosols fall under the Hazardous Waste Regulations because of their residual contents.
Furthermore, depending on the product type, some aerosols may contain irritants or residual amounts of liquids or solids that have other hazardous characteristics that make them harmful, or may be dangerous to the environment.
Magnaflux EMEA therefore recommends the use of a licensed waste contractor for the disposal of Magnaflux aerosols. Please seek the advice of an approved waste disposal contractor for further information.
Further information
The British Aerosol Manufacturer’s Association provides a guide to recycling empty aerosols. This provides guidance on puncturing empty aerosols, so that the hazardous contents can be removed and the metal and plastic components of the aerosol can be recovered and recycled. Note that this should be carried out under the requirements of DSEAR1, and that a chemical risk assessment (COSHH assessment2) of the contents should be conducted. In addition, operatives must be fully trained in the puncturing procedure and must wear appropriate Personal Protective Equipment (PPE).
Disclaimer
The information given in this FAQ is given in good faith, but does not imply acceptance of any liability or responsibility for the consequences of its use or misuse in any particular circumstances.
1 Dangerous Substances and Explosive Atmospheres Regulations 2002
2 A risk assessment of the operation should be carried out in accordance with the Control of Substances Hazardous to Health (COSHH) Regulations 2002 to identify the potential hazards arising from the chemicals likely to be present.
- Does Magnaflux still manufacture the Scrubs hand cleaning towels?
In 2013, the manufacture of ITW Scrubs products for the European market transferred to Kleinmann in Germany. Kleinmann were incorporated into the ITW Group in 2006 and, in 2013, the company merged with ITW Systemcare.
To find your nearest distributor, please visit the Scrubs website.